Report from
North America
Housing starts slow - builder optimism falls
US homebuilding rebounded less than expected in May as
expensive lumber and shortages of other materials
continued to constrain builders¡¯ ability to take advantage
of an acute shortage of houses on the market.
The latest report from the US Department of Commerce
also showed permits for future home construction falling
to a seven-month low. Housing completions also declined
while the number of homes authorized for construction but
not yet started rose to the highest level since 1999,
indicating supply will likely remain tight for a while and
boost house price inflation.
Housing starts rose 3.6% to a seasonally adjusted annual
rate of 1.572 million units last month. Data for April was
revised down to a rate of 1.517 million units from the
previously reported 1.569 million units. Groundbreaking
activity rose in the Midwest, the West and the densely
populated South, but fell in the Northeast.
Single-family homebuilding, the largest share of the
housing market, increased 4.2% to a rate of 1.098 million
units. Starts for the volatile multi-family segment rose
2.4% to a pace of 474,000 units.
A June 15 survey from the National Association of Home
Builders showed confidence among single-family
homebuilders at a 10-month low. The NAHB blamed the
ebb in sentiment on the high costs and unavailability of
building materials.
In Canada, housing starts increased by 3.2% in May.
However, starts in the major cities of Toronto, Vancouver,
and Montreal all trended lower as these markets continued
to moderate from the historic highs they recorded in the
first quarter of the year.
See:
https://www.census.gov/construction/nrc/pdf/newresconst.pdf
Home sales fall for the fourth straight month
Existing-home sales fell for a fourth straight month in May
as prices grew by the most on record. The number of
contracts closed slipped 0.9% in May to a seasonally
adjusted annual rate of 5.8 million from 5.85 million in
April, according to the National Association of Realtors.
"Home sales fell moderately in May and are now
approaching pre-pandemic activity," said Lawrence Yun,
NAR's chief economist. "Lack of inventory continues to
be the overwhelming factor holding back home sales, but
falling affordability is simply squeezing some first-time
buyers out of the market.¡±
The decline in contracts closed in May came as the median
existing-home price surged by a record 23.6% year over
year to US$350,300. Prices have posted 111 straight
months of year-over-year gains since March 2011. For the
second straight month sales were only higher in the
Midwest, where they rose 1.6%. They fell 4.1% in the
West, 0.4% in the South, and 1.4% in the Northeast.
See:
https://www.nar.realtor/research-and-statistics/housingstatistics/existing-home-sales
More jobs added in May but below target
US Job creation disappointed again in May, with nonfarm
payrolls up what normally would be considered a solid
559,000 but still short of lofty expectations, the US
Department of Labor reported.
The unemployment rate fell to 5.8% from 6.1%, which
was better than the estimate of 5.9%. An alternative
measure of unemployment that includes discouraged
workers and those holding parttime jobs for economic
reasons edged lower to 10.2%.
May¡¯s letdown came after April sharply undershot
expectations, with the upwardly revised 278,000 still well
short of the initial 1 million estimate that came with high
hopes for an economy trying to recover from the COVID-
19 pandemic.
The jobs miss comes as employers widely cite a labor
shortage as a critical factor in why more hiring is not
happening.
Some have attributed the situation to generous
unemployment benefits as well as child-care issues and
continuing fears about the coronavirus as obstacles to
filling the 8 million vacant positions. Manufacturing added
23,000 jobs in May, while construction lost 20,000
positions and retail was down 6,000.
Consumer confidence rebounds but inflation fears
remain
Consumer sentiment in the US rose in early June,
according to the University of Michigan¡¯s index,
recouping two-thirds of May's loss. The early June gain
was mainly among middle- and upper-income households
and for future economic prospects rather than current
conditions. Stronger growth in the national economy was
anticipated, with an all-time record number of consumers
anticipating a net decline in unemployment.
Rising inflation remained a top concern of consumers,
although the expected rate of inflation declined in early
June. Spontaneous references to market prices for homes,
vehicles, and household durables hit their worst level since
November 1974. These unfavorable perceptions of market
prices reduced overall buying attitudes for vehicles and
homes to their lowest point since 1982. These declines
were especially sharp among those with incomes in the top
third, who account for more than half of the dollar volume
of retail sales.
¡°Fortunately, in the emergence from the pandemic,
consumers are temporarily less sensitive to prices due to
pent-up demand and record savings as well as improved
job and income prospects,¡± said Chief Economist Richard
Curtin. ¡°The acceptance of price increases as due to the
pandemic, makes inflationary psychology more likely to
gain a foothold if the exit is lengthy.¡±
See:
http://www.sca.isr.umich.edu/
Timber prices retreat from May¡¯s record highs
After a year that saw record-high softwood lumber prices
and shortages nationwide, the price for softwood lumber
has finally begun to drop. Softwood lumber futures
plunged on 10 June to US$1,009.90 per thousand board
feet, down 41% from the record of US$1,711.20 in May
according to the Wall Street Journal.
Before the COVID-19 pandemic it traded in the range of
US$300 to US$500 per thousand board feet. The price
increase was so high, it added about US$36,000 to the
price of a new home, according to the National
Association of Home Builders.
Despite the pullback a projected rise in US homebuilding
will keep lumber prices above US$500 per thousand board
feet for the next five to eight years according to Scott
Reaves, Forest Operations Director at Domain Timber
Advisors.
US manufacturing gains steam; raw material, labour
shortages emerge
US manufacturing activity picked up in May as pent-up
demand amid a reopening economy boosted orders, but
unfinished work piled up because of shortages of raw
materials and labour. The overall economy notched a 12th
consecutive month of growth, say the nation¡¯s supply
executives in the latest Manufacturing ISM Report on
Business.
According to the ISM, worker absenteeism and short-term
shutdowns because of shortages of parts and workers
continued to limit manufacturing's growth potential.
See:https://www.ismworld.org/supply-management-news-andreports/reports/ism-report-on-business/pmi/may/
New Orleans Port rejects Suriname sawnwood
In May, US Customs and Border Protection (CBP)
agriculture specialists at the Port of New Orleans rejected
two non-compliant cargo shipments from South America.
The first shipment was gum rosin from Brazil and the
second shipment was lumber with bark still attached,
shipped from Suriname.
CBP returned the containers back to Brazil and Suriname
because their wood packing materials lacked International
Plant Protection Convention (IPPC) 15 stamps. The IPPC
has an international standard for wood packaging material
to certify that it has been subjected to an approved
treatment measure to keep dangerous insects and their
larvae from burrowing into the wood materials then
escaping the ship or port into the nearby environment.
¡°Inspecting wood packing materials of otherwise lawful
shipments is one of the many, lesser-known ways Office
of Field Operations helps keep our country safe,¡± said
New Orleans Area Port Director Terri Edwards. ¡°An
invasive species can gradually wreak havoc on the
environment and our economy. Just look at the US Forest
Service¡¯s list of invasive insects that have had a significant
impact on the forests of North America.¡±
CBP may issue a penalty for the missing stamps, but
usually brokers are swift to manipulate or re-export the
non-compliant shipment. The costs incurred by the
importer while they wait to get the shipment re-exported
adds up quickly in the port, and there are daily container
charges.
See:https://www.cbp.gov/newsroom/local-mediarelease/unknown-danger-wood-packing-materials-two-mayseizures-port-neworleans?_ga=2.199442734.1045177818.1624495425-1658567841.1624495425
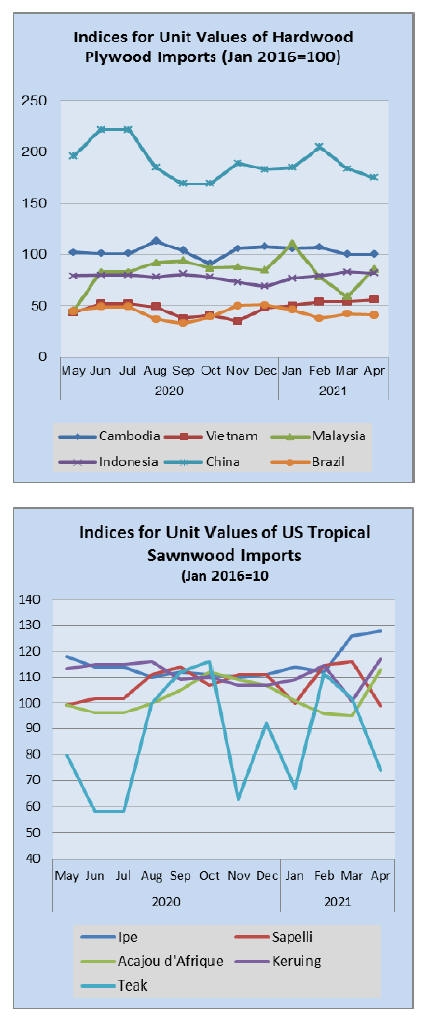
|