Report
from
Europe
No end in sight to recession in EU construction sector
Hopes of a speedy recovery for the European construction industry have
been dashed. Forecasts issued at the latest Euroconstruct meeting held
in Munich during December 2012 suggest that the euro crisis is
continuing to hold European construction activity in check.
Activity is being curbed by high unemployment, stagnant economic growth
or even economic downturns in many places, as well as the strained
financial situation of the public sector.
In June 2012, construction experts from the 19 Euroconstruct member
countries forecast a 2% decline in construction activity during 2012.
However in December 2012, this forecast was revised to a 4.7% decline.
Contrary to their original forecasts, experts now predict further losses
of around 1.6% for 2013 and only minor gains of 1% in 2014 and 1.9% in
2015.
With the debt crisis in Europe*s peripheral countries showing no sign of
resolution, even the minor recovery projected in 2014 and 2015 is
uncertain. Ludwig Dorffmeister of the Ifo Institute, who presented the
overall outlook for the European construction sector at the Munich
conference, said, ※economic developments lead to a change in forecasts
and they are changing all the time.§
Total construction value this year in the 19 Euroconstruct countries is
expected to be 1.27 trillion euros (in 2011 prices). Construction value
in 2013 will be below the level reached in the mid 1990s.
This means that the soaring growth in construction demand seen between
1997 and 2007 has been cancelled out during the six years since 2008.
In 2012 civil engineering looks set to be the most heavily affected with
a decline of around 7.5%. A major factor has been a huge decrease in
construction expenditure by public contracting authorities in Spain.
Downturns in the residential and non-residential construction segments
of 3.5% and 4.2% respectively are less severe but still painful coming
after 4 previous years of stagnant growth. All three sub-segments should
also shrink in 2013.
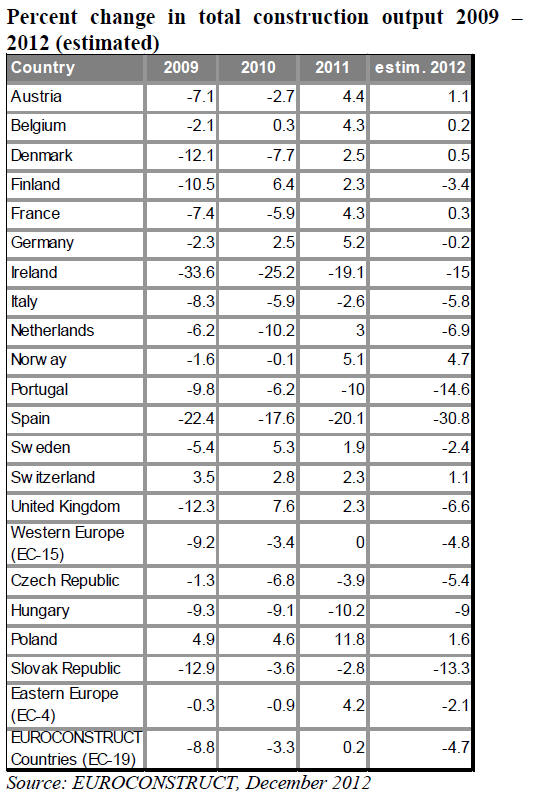
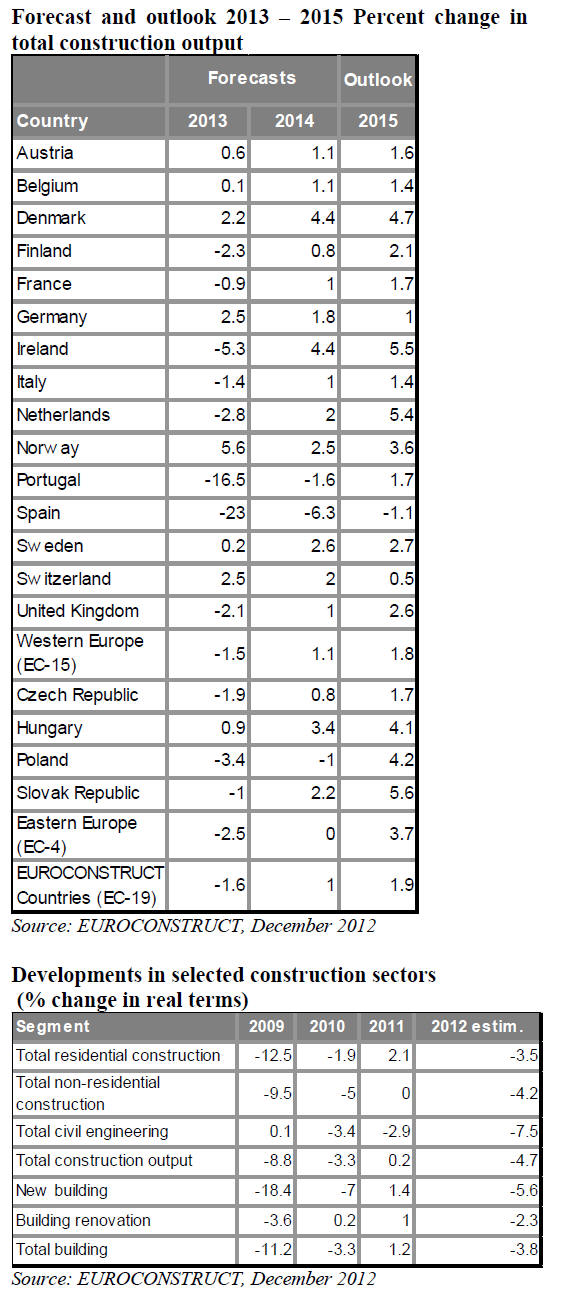
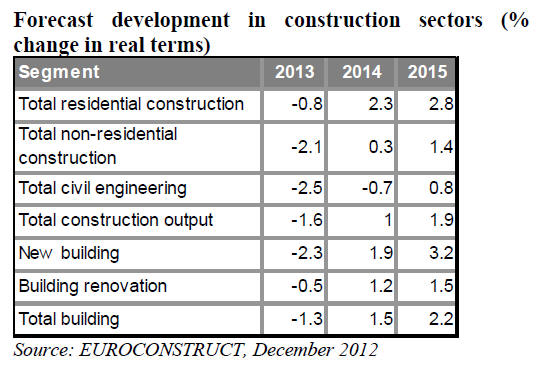
The most distressed construction markets in Europe this year continue to
be the debt-ridden peripheral countries. Spanish construction output
fell by over 30% during 2012. This followed falls of -22.4%, -17.6% and
-20.1% in 2009, 2010, and 2011.
A further fall of -23% is forecast in Spain this year. Portugal and
Ireland also experienced double-digit declines in construction output in
2012.
However, there is moderate growth forecast for some key countries. At
€273 billion (US$ 355 million), Germany is Europe*s largest construction
market. Following a -0.2% decline in 2012, growth in German construction
is expected to resume this year, with a +2.5% increase in output. Low
single-digit growth is also forecast in 2013 for Denmark, Norway, Sweden
and Switzerland.
These countries, with lower debts, are attracting investment capital
thanks to their relative economic stability. Investments in these
countries are focusing on tangible assets, including real-estate.
Moreover, Ireland is currently proving that economic and financial
problems are not necessarily a ※never-ending story§.
Ireland*s improving economic situation is expected to have a positive
effect on construction demand in the near future. After sustaining
serious losses, construction activity in Ireland should rebound in the
next 12 months.
European joinery market under pressure
The downturn in construction sector activity has inevitably led to a
period of uncertainty and tough trading conditions in Europe*s joinery
sector. There is considerable competition between manufacturers of
doors, windows and stair parts. Competition between suppliers of
materials to those manufacturers is also intense.
Wood is under pressure to maintain share following innovations in
plastics, metal and surfacing technologies. With margins so tight, many
wood joinery companies lack the confidence and ability to invest in
future growth.
On the other hand, even in a downturn, European construction continues
to absorb large volumes of joinery products. Those companies with
sufficient capital behind them, which understand and are responsive to
their customers* needs, and which are brave enough to innovate, are
creating new opportunities and increasing share.
A good example is the Howden Joinery Group (HJG), a UK based company
which, according to the Timber Trades Journal, is now the UK*s largest
supplier of kitchens.
The company only began trading in 1995 and now has 520 outlets, 6000
employees, and achieved a turnover of £900 in 2012, a 5% gain on the
previous year.
The company identified that a key trend in the UK kitchen furniture
market was increasing reliance on small local builders for installation.
Do-it-yourself has become less of an option as kitchens have become more
complicated. In response, HJG has developed a huge client list of small
building contractors and property owners across the UK.
The company supplies a wide and customisable range of kitchen components
and provides builders with all the support they need to manage kitchen
installation projects. The company closely monitors consumer trends and
technical developments and regularly develops new product lines. If a
customer wants to return or replace any product, for whatever reason,
it*s done without question.
European manufacturers dominate domestic joinery market
The experience of HJG goes some way towards explaining why Europe*s
joinery sector remains so heavily dominated by domestic manufacturers.
The vast majority of doors, windows, kitchens and stair parts installed
in the EU, are also manufactured in the EU.
Most of the wood material and components supplied into this sector 每
including mouldings, finger-jointed lumber and glulam 每 is also
domestically produced.
External suppliers have struggled to penetrate the European joinery
sector. Success in the sector requires detailed knowledge of changing
consumer tastes and regular contact with a large and generally
fragmented network of building contractors.
It requires responsiveness to customer concerns. Suppliers of joinery
products also need to be willing and able to adhere to an increasingly
complex range of quality and environmental standards established at
European and national level in the EU.
European wood window production boosted by energy efficiency measures
Recent trends in supply of wood windows to the European market are shown
in Chart 1. In 2011, the latest year for which data is available, total
supply of wood windows to the EU was valued at €6.6 billion, 16% less
than prior to the recession in 2007.
The recent downturn is mainly due to a decline in window production in
Italy, Europe*s largest window manufacturing country.
Production elsewhere in Europe has remained quite stable. Stricter
energy regulations introduced in many EU countries has helped create new
demand for energy-efficient windows in Europe over recent years.
This has helped maintain wood window production even as the overall
value of construction has fallen in most European countries.
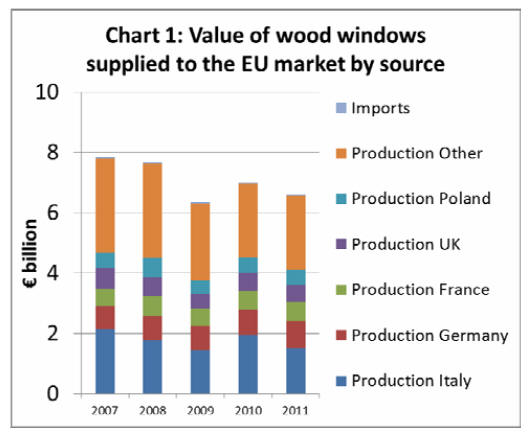
Imports of finished windows make up only a tiny and declining proportion
of the total European wood window market. In 2011, imports accounted for
only 0.5% of the total market, down from 0.8% in 2007.
Chart 2 shows recent quarterly trends in European wood window imports.
In 2011, the EU imported wood windows with a total value of €34.2
million.
China was the second largest external supplier, accounting for €4.6
million (14% of total EU imports) in 2011.
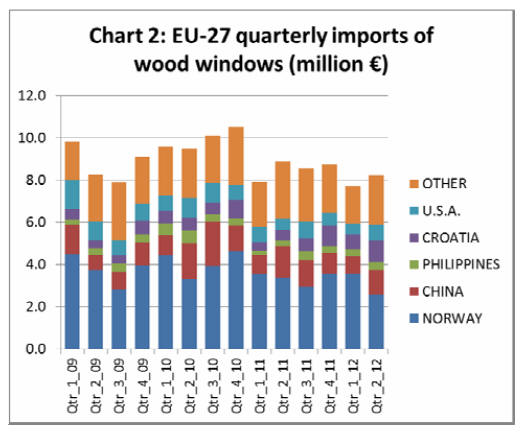
Competition with non-wood materials in the window sector has been very
intense in recent years. Prior to the recession, the overall share of
wood in European window manufacturing fell from around 30% in 1998 to
25% in 2008.
The main beneficiary was plastic which accounted for around 45% share in
2008. Plastics* dominance is due to a combination of low priced product,
strong marketing and distribution networks, and constant innovation to
improve thermal insulation, aesthetics and recycling.
However over the recessionary period, wood windows have performed
reasonably well compared to substitutes. There have been improvements in
the quality of products and services provided by the wood window sector.
There has been a concerted shift to fully factory finished units
offering long service life guarantees.
At the same time, emerging concern for environmental issues and energy
efficiency has helped improved competitiveness of wood windows.
The most widely used wood materials used for windows in Europe are pine
in solid form and laminated spruce. Denser slower growing grades of oak
are also quite widely used for higher value window frames, either in
solid form or increasingly in laminates.
Tropical wood is now restricted to a small-volume high-value niche. Even
in this niche, tropical wood*s position is coming under considerable and
intensifying pressure from alternatives.
Domestic wood dominates material supply to the European wood window
sector. During the recession, the tendency to rely on local species has
tended to increase. Most window manufacturers require timber of
consistent quality to be readily available, increasingly on a
just-in-time basis.
At the same time, the move to fully-factory finished windows has
increased the focus on consistent compliance with very tight size
specifications to avoid wastage and technical standards for strength,
durability, and stability.This is becoming progressively more important
than factors such as versatility and ease of on-site working which have
often favoured imported products such as tropical hardwoods in the past.
These latter trends have particularly encouraged increased use of
engineered wood products in the sector. A few external wood products
suppliers have been able to exploit these trends.
Some Chinese, together with Malaysian and Indonesian manufacturers have
developed and now supply laminated products to the European wood window
sector (see Glulam below).
European door industry declined sharply in recent years
The EU market for wooden doors has declined more sharply than the market
for wood windows in recent years (Chart 3). Total supply of wood doors
to the EU market was valued at €6.3 billion in 2011, nearly 30% less
than before the recession in 2007.
By far the biggest fall in production was in Spain, formerly the EU*s
largest wooden door manufacturer, with total output of €1.71 billion in
2007 falling to only €0.55 billion in 2011.
Wood door production has also fallen quite steeply in UK and France over
the last five years. However wood door production has increased slightly
in Germany during this period, in line with generally more robust
construction activity.
Demand for wood doors in Germany also received a boost from
energy-saving measures. Germany is now Europe*s largest wood door
manufacturer with production value of over €1 billion in 2011.
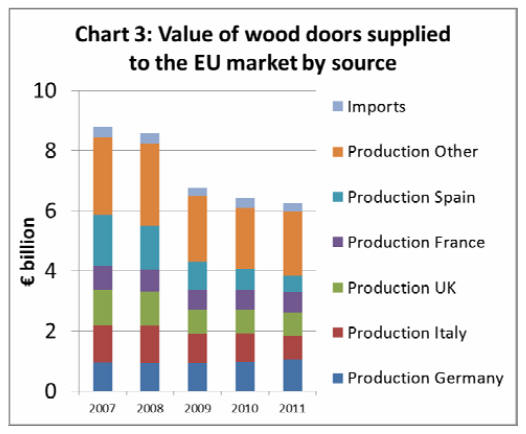
※Real wood§ doors manufactured in Europe are now rarely made from solid
timber and instead are manufactured using veneered panels and
finger-jointed timbers. Doors with a real wood veneer have also been
losing share to doors manufactured using High Pressure Laminate (HPL)
foils and white lacquered products.
This is for various reasons. It is partly due to a shift in overall door
production from Southern European countries such as Spain and Italy,
which strongly favoured real wood veneer, to Germany where there is a
very sophisticated foil and laminates industry. Real wood veneers are
also relatively expensive.
Wood veneer manufacturers also complain that there is a low level of
awareness of the value of real wood doors amongst architects, designers,
and builders merchants.
External suppliers play a relatively small part in the EU market for
finished doors, although their market penetration is higher than in the
wood window sector. In 2011, imports accounted for 4.6% of the total
market, up from 3.9% in 2007.
Chart 2 shows recent quarterly trends in European wood window imports.
In 2011, the EU imported wooden doors with a total value of €290
million. China was the largest external supplier, accounting for €95
million (30% of total EU imports) in 2011.
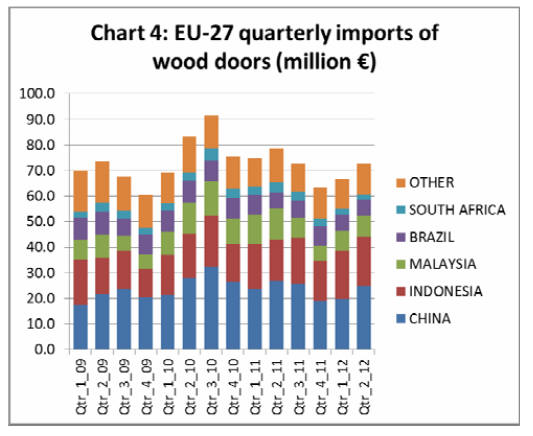
﹛
Glulam increasingly important in the EU joinery sector
There is a strong trend towards increased use of engineered wood
products in Europe. This trend has particularly benefitted Glue
Laminated Timber (Glulam). Glulam, comprising several layers of
small-sized dimensioned lumber glued together into a single component,
is used widely both structurally and for joinery applications.
Glulam offers numerous technical and environmental advantages. Glulam
has a high strength to weight ratio, is naturally durable and robust,
has good fire resistance, and performs consistently and predictably. It
can be used structurally to create vast interior spaces with no internal
supports.
Glulam also allows efficient use of small dimension material to produce
stable, strong and yet light products in a very wide range of sizes.
Glulam has proven particularly well suited to manufacture of modern
factory-finished joinery products conforming to tough quality and
environmental standards and offered with life-time guarantees.
Glulam has also been a major beneficiary of the move to install highly
insulated triple-glazed windows in parts of Europe, notably Germany, as
a measure to increase energy efficiency.
This has required window framing materials that are extremely strong but
also light-weight, a combination of readily achieved by glulam but which
only a few expensive wood species can achieve in their natural state.
Europe is now the world's largest market for glulam, accounting for
close to 60% of all global consumption in 2010. In that year, Europe
consumed around 2.8 million m3 of glulam, down from a peak level of 3.3
million m3 in 2007.
Imports form a small, but increasing, component of overall supply. In
2010, around 135,000 m3 (5%) of EU glulam consumption was imported. The
leading external suppliers of glulam to the EU are Malaysia and
Indonesia, followed by China (Chart 5).
In 2011, EU imports of glulam from China had a value of €22.5 million,
around 17% of total EU imports of €129 million.
﹛
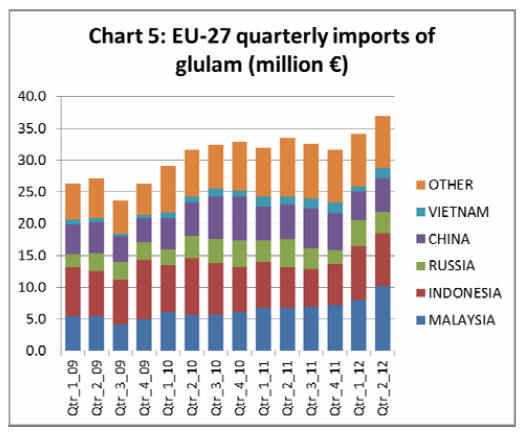
﹛
European glulam producers are concentrated in Germany and Austria. Their
sales are primarily focused on the European market, the only exception
being inter-regional sales to Japan. A large proportion of European
production is focused on spruce as attempts to establish pine products
on the European market have only been partially successful.
Larch glulam has also come to be appreciated by specifiers wishing to
ensure a greater degree of natural durability without the necessity for
pressure treatment. Amongst hardwood species, European oak and American
white oak are most regularly used for manufacturing glulam in Europe.
Hardwood glulam imported into Europe from South East Asia comprises
mainly meranti.
While Germany and Austria have traditionally been the key markets for
glulam, Italy showed very rapid growth in consumption of glulam in the
12 years up to 2010 每 from 100,000 m3 in 1998 to 870,000 m3 in 2010,
after a high of 1,050,000 m3 in 2007.
The rise in consumption of glulam in Italy can be attributed to its use
in the construction of homes, home patios and agricultural buildings.
While the European glulam market has grown over the last decade, it is
currently suffering from saturation. Glulam production in both Austria
and Germany grew steadily between 2000 and 2010, but the increased
production capacity outstripped domestic demand.
Producers therefore focused strongly on increasing exports, notably in
Italy, France, and Japan. However,opportunities in these countries are
now constrained by weak construction sector activity.
Successful participation in the European glulam sector is a complex and
capital intensive process. Supply of glulam is subject to standards
covering the production process, quality control, production
technique/technology, computer-analysis processes, and construction
safety documentation.
The general requirements for glulam are defined in the EN14080 standard.
Mechanical properties are established or experimentally defined with
procedures prescribed in the EN408 standard. Glulam strength classes are
described in EN1194 (Wood Constructions 每 Glued Laminated Timber 每
Strength Classes and Determination of Characteristic Values).
* The market information above has been generously provided by the
Chinese Forest Products Index Mechanism (FPI)
ETTF launches trade monitoring project
The first of a series of analytical reports from the European Timber
Trade Federation (ETTF), designed to monitor the impact of the EU Timber
Regulation on EU timber trade flows, has been launched on
www.ettf.info.
Baseline reports, which can be downloaded, were commissioned from Forest
Industries Intelligence (FII), with funding from the UK's Department for
International Development (DFID) and complement quarterly statistical
reports in the ETTF's Quarterly Newsletter.
The ten baseline reports cover the EU as a whole, and the nine countries
belonging to the ETTF; Belgium, Denmark, France, Germany, Greece, Italy,
the Netherlands, Spain and the UK.
According to report author Rupert Oliver of FII, there are key questions
over the potential effect of the EUTR on the day to day trade of the EU
timber industry, including whether it will make wood more or less
competitive against rival materials, affect demand for certified
sustainable and legally verified products, or divert trade to countries
with less rigorous controls against illegal timber entering their
markets.
The report series will monitor these and other areas, providing vital
information to both businesses and national and EU authorities involved
in the implementation and enforcement of the EUTR.
Subsequent reports will include in-depth interviews with traders, as
well as statistical analysis, to assess the extent of changes in the
trade after the EUTR comes into effect.
﹛
|